£0.00
0FAQs
BIL Group
− Do your ranges come with a warranty?
Yes they do! Our ranges come with a 12-month warranty as standard.
− Do you offer account facilities?
If you feel BIL is right for your business (we can’t find a reason it wouldn’t be!) then yes we do provide account facilities! Our standard terms are 30 days and all it takes is a couple of forms to be completed! If you would like a copy of these forms then please contact us.
− What payment methods do you take?
We accept credit cards, debit cards, PayPal, G pay and Apple pay. You can also spread your cost with 3 interest-free payments through Klarna. More information is available on our "ways to pay" page.
− What is your returns policy?
This is stated within our terms and conditions.
− How quick is your delivery time? Is same day delivery available?
For website orders, please allow up to 3 days from the order date. Next day delivery is available for some items, please contact our sales team on 01249 822 222 if you wish to discuss this.
− Do you offer discounts?
Potentially yes. Please contact our sales team on 01249 822 222 to discuss our possible discounts, or sign up to our email list for the latest news and offers.
− Do you accept overseas orders?
Yes, we do. Please place your order through the website in the normal way, or you can call us to place your order on 01249 822 222.
− Do you offer site visits to help with my requirements?
Yes. Our external sales team can visit your site, discuss your requirements and run through the options available. They can also bring samples to your site for trial. This service is available for customers who are looking for a large quantity of products. Please call to arrange a demonstration on 01249 822 222 or complete our online booking form.
− Do you offer bespoke products?
Yes - we are able to offer bespoke products. Please call us on 01249 822 222 to discuss your requirements. We’d love to hear from you.
− How will my order be delivered and how much will I have to pay?
We will send your order by the most efficient method. However, certain sizes and weights may require specific carriers to be used.
Free collection from our warehouse in Calne, Wiltshire, is always offered.
For delivery information inside and outside of the UK, please visit our delivery and returns page.
Palletised Shipments
Items that are too heavy or too large to be transported by standard methods will be sent by pallet. If this is the case for your order, you will receive a freight quote. You may need to provide assistance for unloading individual items over 30kg.
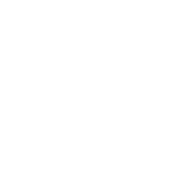
BIL Group
Frequently asked questions about us, the company and our service.
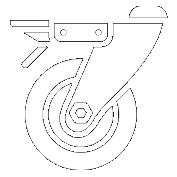
Castors and wheels
Frequently asked questions for our castors and wheels products.
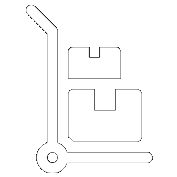
Materials Handling
Frequently asked questions for our materials handling products.
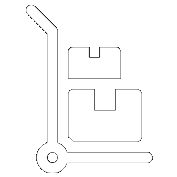
Alutruk
Frequently asked questions for our alutruk products.
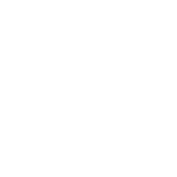
Skoots
Frequently asked questions for our skoots products.